BLOG
Benefits of Thermal Imaging in RoofingThermal imaging technology has revolutionized the way roofing inspections are conducted, providing numerous advantages over traditional methods. With the capability to detect roof leaks and assess the overall condition of a roof with precision and efficiency, thermal imaging technology has become an indispensable tool for roof maintenance professionals.
RAM Infrared Services, a leader in the field of thermal imaging technology, offers comprehensive solutions for roof inspections that deliver accurate results and help property owners and managers prevent costly repairs. Read on to discover the advantages of using thermal imaging technology in roofing inspections.
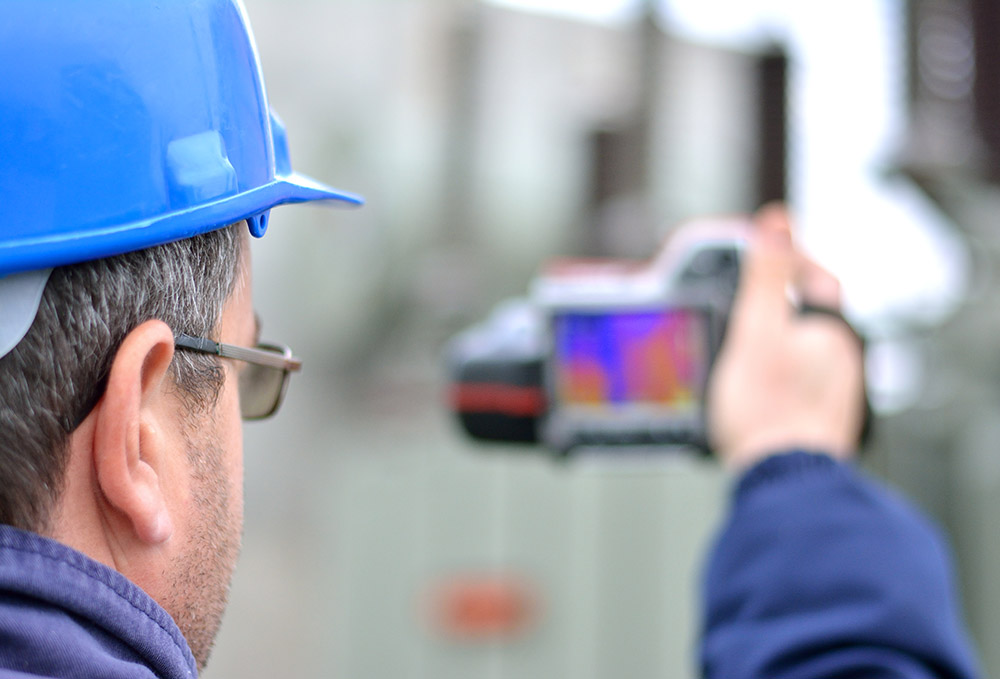
How does a thermal roof inspection work?
Thermal imaging technology in roofing inspections involves the use of infrared cameras to capture images of a roof’s surface temperature variations. These cameras detect thermal energy emitted by objects and translate it into visible images, allowing inspectors to identify moisture, leaks, and insulation gaps that are not visible to the naked eye.
A thermal camera is able to detect areas on a roof that are holding moisture because wet areas cool at a different rate than dry areas. When the sun sets or the temperature drops, the roof begins to cool down. However, areas that are wet will retain more heat and cool down slower than dry areas. This temperature difference is detected by the thermal camera, allowing it to identify the areas that are holding moisture. This difference in cooling rates helps the camera to pinpoint the specific areas on the roof that may be damaged or need attention due to moisture buildup.
By analyzing these thermal patterns, professionals can pinpoint potential issues early on, preventing extensive damage and reducing repair costs in the long run. This innovative technology provides a non-invasive and efficient way to conduct thorough roof assessments, making it a valuable asset for property maintenance.
Advantages of Roof Infrared Scans
Utilizing thermal imaging technology in roofing inspections offers numerous benefits. Firstly, it provides a comprehensive and accurate assessment of the roof’s condition by revealing hidden issues such as moisture intrusion and insulation deficiencies. This early detection capability enables timely repairs, preventing further damage and costly repairs down the line. Additionally, the non-invasive nature of thermal imaging reduces the need for destructive inspection methods, preserving the integrity of the roof. Moreover, the efficiency and speed of thermal inspections save time and resources for both inspectors and property owners. Overall, incorporating thermal imaging technology in roofing inspections enhances the safety, sustainability, and longevity of the roofing system.
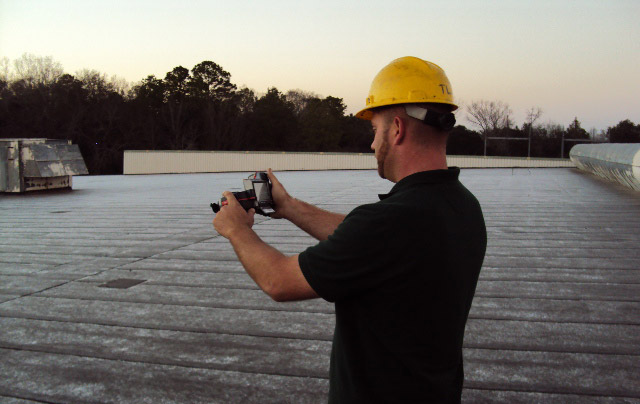
Benefit #1 – Improved Safety for Workers
When moisture gets trapped in your roof system, it can lead to the corrosion of the metal components or the decay of the wooden roof deck, which in turn can weaken the overall structure of your roof. If left untreated, rotted or rusted roof decks can create a hazardous environment for workers who need to access the roof for maintenance or inspections. This not only poses a safety risk for workers but also increases the likelihood of costly repairs or even roof collapse. It is crucial to regularly inspect and maintain your roof to prevent moisture buildup and ensure the longevity of your roof system.
Benefit #2 – Prevent Interior Damage and Mold Growth
Water intrusion in your roof system is not just a small annoyance – it can have serious consequences for your building. Leaks in your roof can result in interior damage, impacting critical electrical and mechanical systems. This can disrupt operations and damage inventory, leading to costly repairs.
Additionally, trapped moisture in your roof can lead to the formation of mold. Mold not only poses health risks to occupants of the building, but also can cause further damage to the structure and decrease its overall value.
Preventing water intrusion in your roof system is essential to maintaining the integrity of your building. Regular inspections and maintenance can help identify and address issues before they become major problems. Investing in high-quality roofing materials and proper installation can also help protect your building from water damage.
Roof infrared scans are a valuable tool in preventing interior damage to a building. By detecting leaks and moisture early on, building owners can take the necessary steps to repair and prevent further damage. Investing in regular roof infrared scans can help save money, protect the structural integrity of the building, and ensure the safety and comfort of its occupants.
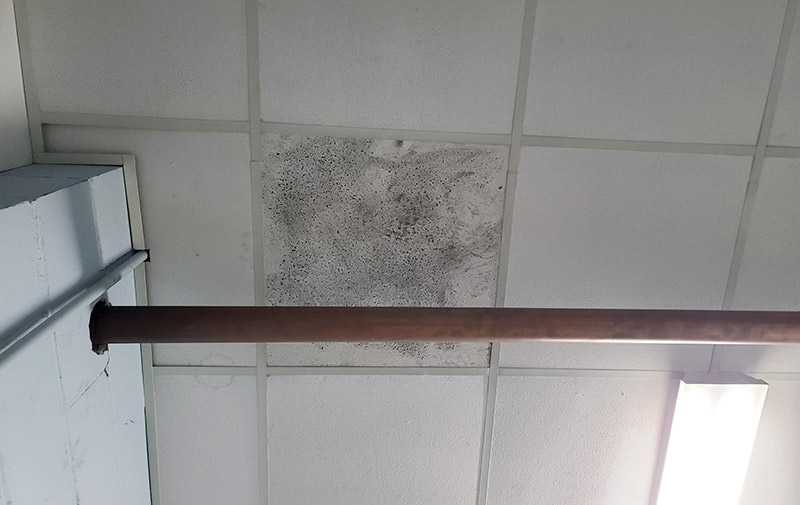
Benefit #3 – Increased Accuracy in Identifying Roof Issues
Thermal imaging technology enhances the accuracy of identifying roof issues by providing detailed images that pinpoint areas of concern with precision. The thermal images captured during inspections clearly highlight temperature differentials, allowing inspectors to detect specific problems such as moisture trapped beneath the surface or insulation gaps.
This level of specificity ensures that all potential issues are properly identified and addressed promptly, leading to more effective repairs and maintenance strategies. By leveraging the increased accuracy of thermal imaging technology, roofing professionals can deliver superior results and ensure the long-term integrity of the roof structure.
Benefit #4 – Time and Cost Efficiency
In addition to improving accuracy, thermal imaging technology also offers significant time and cost savings for roofing inspections. The detailed images provided by thermal cameras enable inspectors to quickly identify and assess problems without the need for invasive and time-consuming manual inspections.
This efficiency not only saves valuable time but also reduces labor costs associated with traditional inspection methods. By streamlining the inspection process, thermal imaging technology allows roofing professionals to complete assessments more efficiently, allocate resources effectively, and ultimately deliver cost-effective solutions to their clients. Embracing thermal imaging technology in roofing inspections is not only a smart choice for accuracy but also for maximizing efficiency and minimizing costs.
Then there’s also the costly endevor of a roof replacement. By using this technology, you can detect issues such as wet insulation before they become major problems. Regular infrared scanning of your roof is a cost-effective way to monitor the health of your roof and address issues as soon as possible while they are still relatively easy to repair, such as wet insulation remediation.
Benefit #5 – Help to Lower Your Building’s Energy Costs
A commonly overlooked aspect of building insulation is the impact of moisture on its effectiveness. Wet roof insulation can lead to increased heating and cooling costs for your building. This is because wet insulation conducts thermal energy better than dry insulation, which means that heat can escape more easily in the winter and enter more readily in the summer.
One of the main roles of insulation is to resist the flow of heat, keeping the temperature inside your building stable and reducing the need for excessive heating and cooling. However, when moisture infiltrates the insulation, it compromises its ability to do so effectively. Wet insulation conducts heat at a much higher rate than dry insulation, essentially acting as a bridge that allows thermal energy to pass through more easily.
Regular infrared scanning allows you to catch issues before they escalate, making repairs easier and less expensive. By investing in this preventative maintenance, you can extend the life of your roof and ensure that your building remains energy efficient.
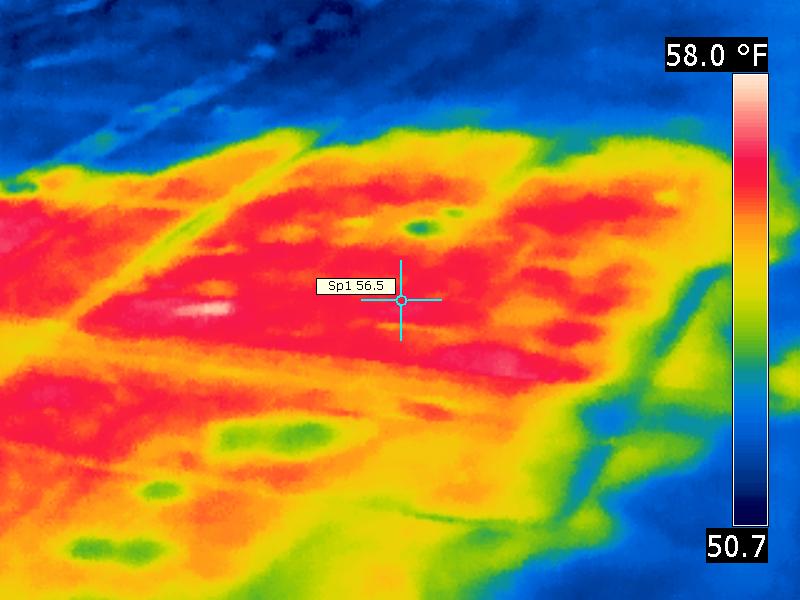
Benefit #6 – Help Protect your Roof Warranty Status
Many roofing manufacturers now require regular thermal imaging as part of their warranty agreements. By conducting scheduled thermographic inspections, you can ensure that any potential problems are identified early on and addressed promptly, in compliance with the manufacturer’s guidelines. This not only protects your warranty coverage but also helps you maintain the value of your investment in your roof system.
Beyond warranty requirements, the benefits of thermal imaging for your roof system are numerous. By proactively identifying and addressing issues, you can extend the lifespan of your roof, reduce energy costs, and improve the overall performance of your building. Additionally, thermal imaging can help you prioritize maintenance and repairs, making them more cost-effective and preventing potential damage to your property.
Conditions Necessary for a Successful Thermal Roof Scan
One word of caution before you dive into hiring a contractor to perform a thermal scan of your roof. There are certain necessary conditions needed to ensure a successful thermal scan of your roof. If the conditions are not correct it can render the scan useless.
One crucial consideration is the weather conditions. A thermal scan requires stable weather conditions, preferably on a clear, sunny day. Rain, snow, or extreme temperatures can alter the surface temperature of the roof, affecting the accuracy of the scan. It is important to schedule the thermal scan during a period of ideal weather conditions to ensure reliable results.
In addition to weather conditions, the time of day can also impact the quality of the thermal scan. Thermal roof imaging works by reading temperatures of the roof surface and therefore needs to be performed during the right conditions to ensure an accurate reading. Based on these conditions there are two types of surveys that can be performed with thermal imaging:
Warm weather scans use thermal imaging to read the difference in temperature between wet and dry roof insulation. These types of roof moisture surveys are performed during warm weather after the sun has set. As the sun heats the roof during the day it also heats the wet insulation. After the sun has set and the dry portions of the roof begin to cool, these wet areas will hold the heat and that’s when you begin to see these areas as “hot spots” with a thermal imager.
Cold weather scans are done during cold weather or possibly early morning throughout the year. This type of survey is based on the difference between indoor and outdoor temperatures. Since wet roof insulation has a higher thermal conductivity than dry insulation when the inside of the building is warmer than the air outside the wet insulation will transfer more heat out of the building than dry insulation.
Additional Tools
The moisture meter is another tool used in conjunction with thermal imaging to confirm the presence of moisture. A thermal imager alone cannot verify the existence of moisture; it works more as a guide to read the thermal signature of the roof surface to discover the areas where it appears there is moisture. It still requires a certified technician to in fact verify and locate the exact area.
There are 2 types of moisture meters – penetrating and non-penetrating.
Penetrating moisture meters have one or a series of pins that probe into the surface of the roof to capture the moisture content values. They tend to sometimes be more accurate than non-penetrating meters, but they also do just what they say, penetrate the roof surface which will then need to be repaired.
Non-penetrating moisture meters are non-invasive and will not create damage to the roof surface. They contain a series of sensors that measure the moisture levels through the system. Even though they may not be as accurate as the penetrating moisture meter, they are still very accurate and can verify moisture in a roof system without penetrating the surface.
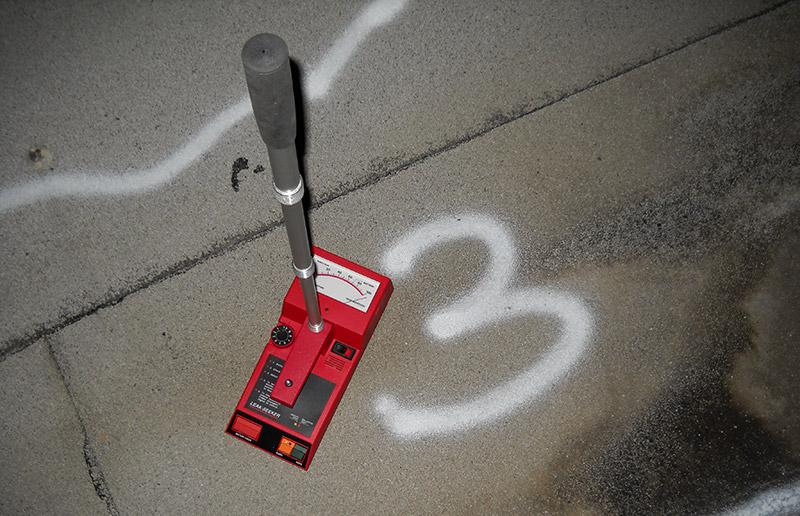
Thermal Roof Scan Limitations
As effective as thermal imaging can be it does have its limitations. Variable weather conditions and differences between types of roof systems can render these scans ineffective. It’s important to have a certified technician to help ensure the scan is effective.
Issues such as lack of solar load, high winds and heavy dew make it difficult to detect thermal patterns within a roof. As far as roof types, heavily ballasted roof systems are not a good candidate for thermal imaging along with roof systems containing more than one layer of insulation. Also inverted membrane roofs are not typically inspected with thermal imaging.
Moisture meters also have limitations. EPDM roof membranes have a high carbon content which registers them as wet on the non-penetrating meter. Infrared can be used with EPDM but confirming the areas that may contain moisture may need to be completed with a penetrating moisture meter.
Again, it’s important to hire a competent and certified thermographer to complete your roof moisture scan. Make sure your technician is certified by a credible institute such as Infraspection Institute.
Conclusion
In conclusion, the benefits of incorporating thermal imaging technology in roofing inspections are undeniable. From ensuring accurate evaluations to enhancing safety measures, this advanced tool revolutionizes the way roofing and consulting professionals operate.
As the roofing industry continues to evolve, embracing technological advancements like thermal imaging will undoubtedly set companies apart and solidify their reputation as industry leaders in delivering top-tier roofing solutions.
Related posts
Unlocking a New Era of Infrared Inspections: RAM Infrared Adds DJI Matrice 4 Series to Its Fleet
RAM Infrared Adds DJI Matrice 4 Series to Its FleetAt RAM Infrared, we know our clients depend on us for more than just thermal imaging—they rely on us for answers. Fast, accurate, actionable insights are the backbone of everything we do. That’s why we’ve expanded our...
Aerial Drone Roofing Services: The Future of Inspections and Thermal Scans
The Future of Inspections and Thermal ScansThe roofing industry is experiencing a technological revolution with the adoption of aerial drone services. These cutting-edge tools are reshaping how inspections and maintenance are performed, offering unparalleled...
Aerial Infrared Imaging: A Cutting-Edge Solution for Roof Surveys
A Cutting-Edge Solution for Roof SurveysAs a commercial building owner or manager, ensuring the long-term health of your building's roof is crucial for protecting your investment. Traditional roof inspections, while effective, can sometimes be labor-intensive and may...